Exponential wobble man; that sounds like my favorite bass music
“So the best place to scale first is with the tracks length.” @roryaronson - So the spiral is definitely the way to go as far as a simple innovation - provided that there’s not a significant technical issue. Whether you; convert your algorithms into a polar coordinate system, or use some type of digital imaging to map your current cartesian system, I think its do-able with existing tech and software.
“The other option is a cantilevered arm that is supported by guide wires from above, like a suspension bridge.” Hmmmm yesh. Imagine a 1.5 m wide spiral bed with this design, the setup cost could be very low. if we can get even 30 m away from the central power/water “station” thats a significant amount of area. This answer is very approximate but (3.143030)*.67 = 188.5 m/sq with one print head and one power/water station, and rigging set? How’s my jackalope math folks?
Hello, I´m new to this board and excited about the potential of this project! I work in a riverdwelling community in Brazil and we have been considering new gardening system that is working well in other parts of this country. When I saw the video on facebook about the FarmBot, the first thought that crossed my mind was: could this be done in a circular fashion? I will include an image of the system I´m talking about. Although I do not understand much about the tecnology behind FarmBor, it would be interesting if FarmBot could be developed in such a way to help low income families increase their production, even without much knowlege about growing. It would also be interesting to have the system function off solar panels too, bc many of these people are off grid and have no access to (much less could afford) electricity.
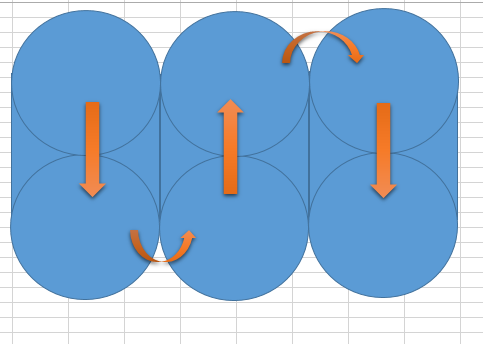
What if instead of an outer track, having wheels directly in the ground with a motor being able to move forward or backwards the entire arm?
Additionally, if the central point base is also powered by a motor, the entire framework could be moved around, with the support of Beacons to locate the central point of the next circular plant. It would allow the entire framework move around to all circular plants of the farm.
So, central points would be a grid to provide energy power and water. Am I gonna too far?
Farmers install pivots for watering because circles are the most efficient/automated way to water crops in a field. The pivots have electricity, water, and wheels that moves everything around
Someone should get a hold of one and load up the spans between the wheels with these gantries. The existing watering could be left in place (or not. the wheels move very slowly), leaving the bots to handle seeding and weeding.
That would be a fascinating project for any farmer, but not for most homeowners.
totally viable, great idea if you’re using hothouses, hoop houses or your green house is long - also can be done within the cartesian platform i believe
Hmmmm… I wonder about this… great idea with mega advantages for sure … I think it would require moderate development. If you have a track on one side and a wheel on the other, the ground would have to be super flat - there’s torsion, shimmy or bumping could click or lock on the tracks. I think this idea, eventually is a better more robust system - but wayyy easier with wheels on both sides no rails. you could definitely get a heavy piece of gear rolling around on two wheels =-p Hell thats a good idea for an “ecological restoration” bot
Great discussion everyone! I think polar coordinate bots are definitely possible, and there are many ways to go about it. If anyone decides to start designing/building one, feel free to make a thread about it in the forum. I think all it would take on the software side is a firmware level conversion from cartesian to polar coordinates in order to position the tool head correctly. For hardware, there are obviously many solutions, and probably different designs will be better or worse at different scales. Looking forward to seeing the prototypes!
Great community here! Just starting to read everything. For the sake of internationality - could you please use SI units? Best regards, m2k1
I, too, am new to this site and I have a small veggie garden in N. Ireland. Watering is NOT a problem!! But I will be putting one in my Polly Tunnel.
The easiest way to double the growing area is to have the gantry’s home position in the middle of the two beds. No extra work required as the travel is still the same. And the code changes are just a “mirror” of the main code, with some minor changes are the tool station would now be directly below the gantry.
It’s quite interesting that I should come across the FarmBot because for the past couple of years I have been working with all the Pi devices as well as the Arduino’s and I love to grow veggies! I also have my blog that I publish my articles on the stuff I am doing, it’s (if the link is OK with admin) jonstephensonsblog.me.
I have a LOT of reading to do!! I’ll look for the correct place the next part: The downloaded Arduino code fails to compile, with a ‘PinGrardPin’ does not name a type…
Since hearing about this project I’ve been obsessing over expanding the scale and here are my ideas:
The existing design is fantastic and should scale easily with only minor modification. I’d suggest you keep the existing Cartesian alignment system and extend distances with two methods: untether the gantry system and add a means of track switching for lateral relocation.
Untethering the gantry would remove the cost of X-axis cable carrier, but introduces a load of problems to replicate the delivery of supplies. The necessary supplies at present are: power, water and vacuum. I propose that these be supplied by a motorized trailer. The trailer would look similar to the gantry but would have deep cycle battery and vacuum on one vertical, a water tank and pump on the other and possibly a solar panel across the horizontal. The trailer would obviously be much heavier than the gantry but would not need precision in its location. So instead of stepper motors, it would simply have relay controlled standard motors designed to keep it within say 1 meter of the gantry based on the max length of the connecting systems. This need for the extra weight would tax the rail system, but I think this necessary as I think the best harvesting system on a long bed would be a prone human on a powered trolley as this would also eliminate the need for space between the rows which maximizes growing space and eliminates soil compaction. It also halves the number of rails necessary as each rail would now edge two beds.
Now that the gantry is untethered you could link parallel rows by a separate perpendicular rail system that would effectively act as a horizontal elevator and resupply station. The second car system would have extensions of the standard rails large enough to contain both gantry and trailer with hookups to recharge the battery and refill the water tank. The second rail system may also need a Z-axis alignment system to account for height changes between rows.
I think with the addition of these two systems you could use a single farmbot to support nearly an unlimited area with the limitation being water supply delivery time. If the rails are designed to support a 90kg person for harvesting then up to 40kg of water would be significant as it would only be used as needed before the gantry and trailer would have to go back and be refilled. Since the Farmbot can work 24/7 this shouldn’t be a major limitation in all but the largest greenhouses or driest locations.
What do you think?
I like the extra set of rails to service multiple beds. It’s actually something I came up with in another thread so it’s re-assuring that someone else is also playing with this idea. I can’t wait to play around with my own kit.
@RichardJHauser I think the easiest/lowest cost way to expand the system is by extending the tracks. We’re working on larger devices and extension kits to be released in about a year. We might actually be able to offer extension kits before we ship in February, but no promises! As you mentioned, the main challenge is the delivery of supplies.
Vacuum and power are easy - just put a solar panel and battery on the gantry, as well as the vacuum. You would need to upgrade the gantry motors to move the extra weight around, but that’s really it.
An idea I had for water delivery over long distances is an aqueduct/trough that runs along the bed. FarmBot could then have a pump and a “straw” that sucks up water from anywhere along the trough/bed.
Another idea is “water stations”, like how steam trains used to have! So FarmBot would have a small on-board water tank which it could refill from a number of stations spaced throughout the growing area.
I like the watering stations idea! With a miniature microwave and syringe you could water the plants and remove weeds with boiling water at the same time!
This is not small enough, but is heading in the right direction!
Speaking directly to the issue of carrying more weight.
The two thought I have are;
Cable weight: Abandon the whole track cable guard thing. Suspend cabling on a upper track or taut cable with pulleys supporting the weight at intervals (1-3 meters?).
Torque boost: As far as I see it, right now you have a couple of stepper motors that are not being utilized enough. Someone with more knowledge would have to connect the dots but I think you should work gears, pulleys, or belts so that all the gantry arm’s steppers will be engaged to help move the gantry around. In other words if I understand the way it is now, one or two steppers move the gantry up and down the track. If you rework it where even the z axis provides its torgue for movement when its not being used for its main purpose then you should get a lot of previously wasted torque back.
An example of an alteration would be to move the z axis stepper to the base of the arm it is on now (this should also help with wobble caused by its weight) and just use a different shaft that allows it to run perpendicular. Then another shaft running to the end of the top part of gantry could have a gear that allows the torque from a couple of different sources to be added in. To switch between the two the stepper would either have to move or a dear added and controlled at the stepper z axis shaft that would disengage the one shaft and engage the other.
Now it might be much simpler to just upgrade the steppers but I dont think it would hurt to keep thinking and imagining along these lines to squeeze more efficiency out of any device.
I for one would like a beefy gantry, it matches several of the mod ideas for the wants and needs of several people and would provide much more versatility (imho) in the end. Also it would solve more then one issue. Like the vacuum pump would definitely be on the gantry then (on the sides) along with other needed mods. The stability issue would be a lot less than as well.
Who votes for a Gantry like a tank? I do!!
The way I see all of this scaling up is going to be restricted to the small to mid sized operations. Trying to put tracks, and the the infrastructure with them in huge fields isn’t practical. Fully automated tractors are probably going to be what big ag ends up using. Sorta the point of farmbot is taking food production out of the hands of big ag and giving it back to us.
I think the best place to scale farmbot up more than now would be using the existing infrastructure in long greenhouses. Mount a monorail ganty from the existing ceiling infrastructure and lose the side rails. All three axis motors would be mounted on the gantry.
I had the same idea as Roy with having a water trough that the bot just dips its hose into to suck water up from. For adding fertilizer it could carry concentrate on the gantry and mix it in as it goes for each specific plant.
Either carry the vacuum pump, go to a mini air compressor with a venturi vacuum(this should solve the seeds in your vacuum pump issues), or use a seed shaker(will post about this idea on another thread) and eliminate the air hoses completely.
Getting rid of Water and air hoses leaves only a need for power, and electricity isn’t as heavy :P. For those remaining power cables, tug them along with a cable festooning system similar to this.
Put the festooning system either on the main rail, or better yet have a secondary rail next to the bed that the cable/remaining hoses travel on. You could even tug along the tool bay on the festoon rail so you don’t have to run back along your super long bed.
And for a long multi bed greenhouse, at the end of a line swing the robot gantry around to the next bed with a curved U-rail and start coming back the way you came on the new bed. If the cable festooning is on a separate rail it can now start to bunch itself back up. The trick to adding more than two beds would be figuring out a simple system for moving the festoonig system between rows. But I am sure it can be done with some simple track work.
lol excuse my mspaint engineering, but I made a quick diagram of what the layout would look like. Red is the main overhead gantry with the bot, green is the festooning system, and blue is the water troughs it pulls from.
Not sure about the feasibility but where I work there is track power so if you wanted to you could get rid of the power cables. Then if you make the data wireless then basically no long length cables. The rail would have semi-overlapping rubber flaps that the arm would open and close behind itself to keep it more weather tight.
If you worry about inconsistent power on the rail because of movement you could have them run through a cap that is recharging a battery that the boards and such draw from.
I also would like to say if someone was to make a ceiling railed powered system with wireless data, water and fertilizer troughs, I would then think it would be a great idea to have multiple upper mounted rails set close enough that they both would be able to reach the whole bed.
Then instead of worry about how many passes with a tool you can have in a 24hr period, you would just need to decide how many rails you wanted to run. This would allow for the manual version of the weed killer which would have plenty of time to beat the weeds into submission.
Any additional cost from adding the above mounted railing and extra arms would be offset from not having to have the ground mounted rails.
It would also provide a place to add shades or reflectors to help the people with too little or too much sun.
You could have the rails in smaller sections with multiple arms as well if that suited the situation better.